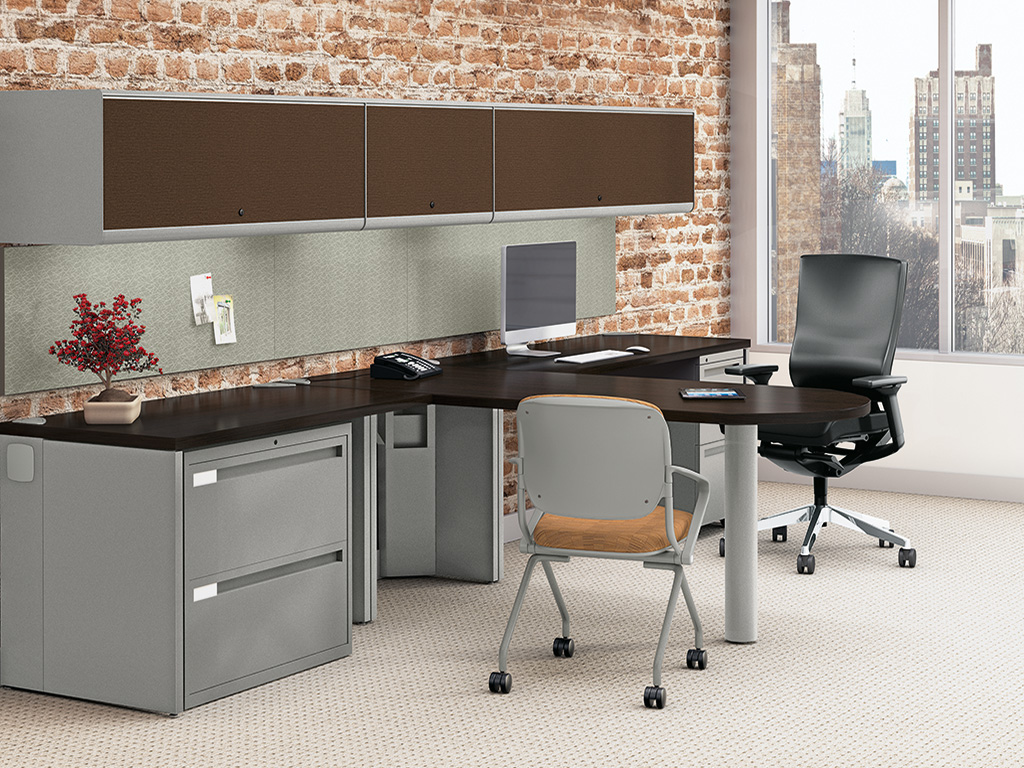
I got bored of my job at the garage. There was an entire week of no work. Also the inmate who knew the most was not a good teacher and very critical and demeaning. He has been in prison for several years and has several more to go. I heard some inmates who are supervisors do this and take their depression out on others. I didn’t want to deal with this negativity for another 4.5 hours each weekday. Typically I would need to wait 90 days to change jobs with my manager’s approval. This can be challenging for someone they don’t want to lose and has been there a while. I decided to confront my manager after only 3 weeks and explained the job was not working out and it would be a waste to continue to train me. After one week in limbo, I got his approval to switch jobs and started a new job at Unicor the last week of December. My neighbor explained his job at Unicor and put in a good word for me and they immediately took me on. Apparently, they seem to try anyone so it wasn’t like the references I put on my paperwork likely made a difference.
The BOP created Unicor to employ inmates with jobs they can use at a real world business, rather than the standard prison maintenance and operation type jobs, which support our day to day lives at the camp (food service, janitorial, maintenance, landscaping, etc). This lowers recidivism and they do focus on that with most programs. You can read more about Unicor here. There are no Unicor jobs onsite at Lewisburg. We are shuttled in 2 vans and a SUV to and from a warehouse on the edge of a neighboring federal prison complex in Allenwood. This Unicor location handles office furniture and electronics recycling. The warehouse is just like any other warehouse in the free world and doesn’t have a perimeter fence. The complex consists of a low, medium, and high security prison, all of which have significant perimeter fencing, walls, and prison cells. I currently work in the office furniture area and the primary product is premium computer type office chairs. Here are the different chairs we put together: see types here. They also make simple chairs along with office couches. Here is the chair type that is in the visitation room: grazie chair with the sled. Four manufacturers ship in trailer loads of parts and boxes. The pallets of boxes are unloaded and put into inventory. Government customers all throughout the US (Navy, Airforce, prisons, etc) place custom orders with our division. SAP software manages everything including the parts needed to build the chairs. The warehouse staff prints out a pick list, picks the parts needed, puts them on pallets, then uses forklifts to move and wrap the pallets and load them onto trailers. The trailers are sent into the low prison and those inmates unload the trailers, assemble the chairs, box them up and load them on trailers to return to the same warehouse we are in. The other side of our warehouse unloads the finished chairs and couches and stores them in the warehouse until the customer is ready to receive them, which could be months out. The warehouse is very full of orders that were made, paid for, but are not ready to ship. The chair boxes are bulky and just moved around with hand trucks. Lots of labor, but that is a very low cost for Unicor.
I’ve been learning how to use the SAP software for receiving and picking orders. I’ve also been learning the various parts and locations, helping to pick the parts and load/unload trucks. Once my computer access background check is complete, I will be able to assist a little more. There are already two clerks that use the computers on the parts side of the warehouse, but they are good with cross training extra folks since there is turnover as inmates leave. My official position is QA, where I help with parts that break and need to be replaced typically found during assembly. My supervisor, managers and head of the division at Unicor are very nice to work with. We still don’t stay that busy, but I like this new job better than the previous one.
Leave a Reply